Collaborative Partnerships
At MES, we believe that successful product development is built on strong partnerships. We work closely with our clients throughout the entire development process, from initial concept to final production. Our collaborative approach ensures that we deliver solutions that meet the unique needs of each customer.
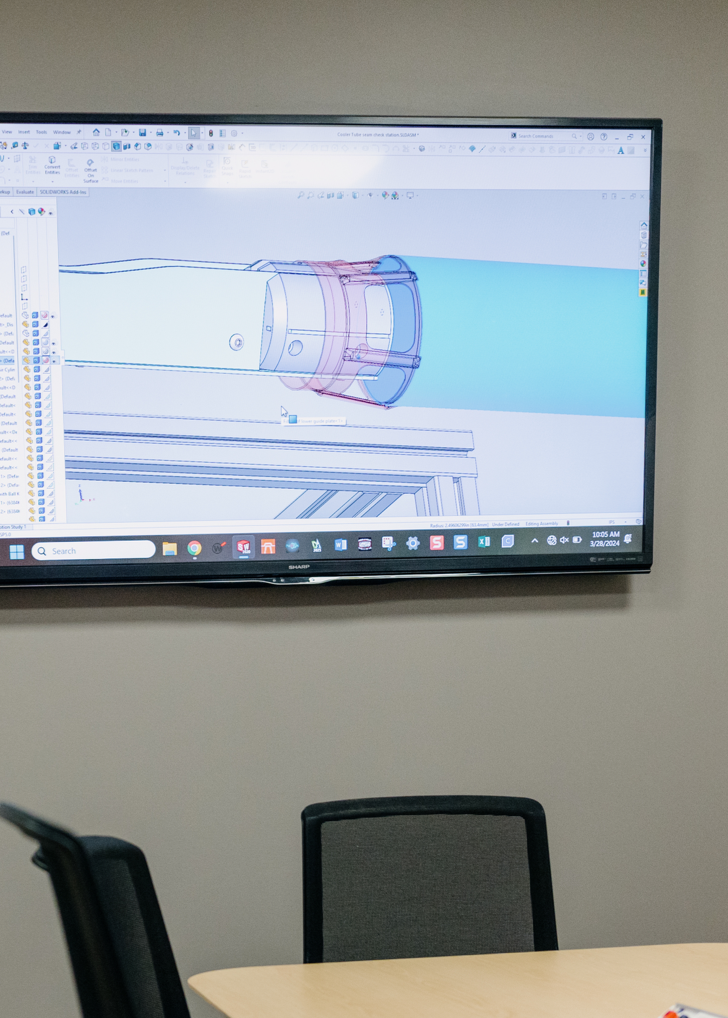
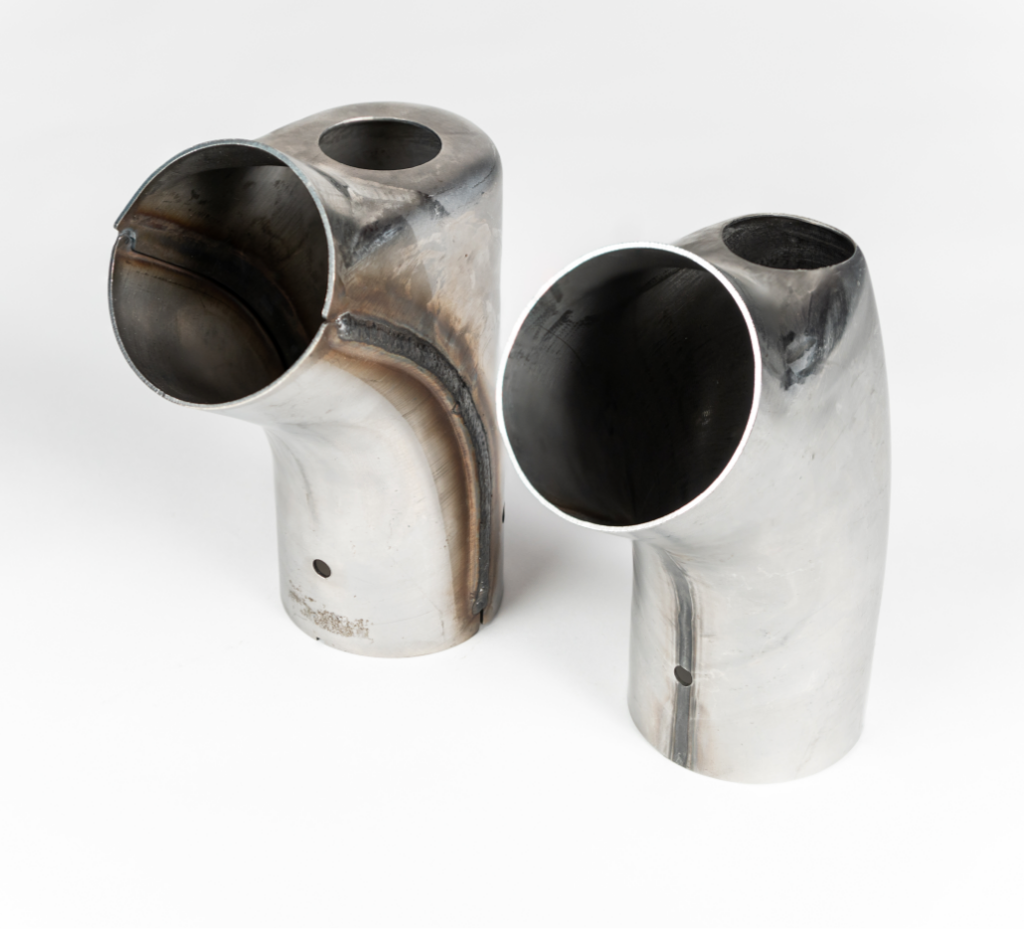
Driving Innovation Across Industries
Our product development expertise spans a wide range of industries, including automotive, aerospace, healthcare, consumer goods, and more. No matter the industry, MES is dedicated to providing innovative solutions that drive success and set new standards of excellence.
Comprehensive Development Process
Serving as an extension of our customers’ engineering teams, MES has created a unique process for developing and implementing solutions not commonly found in the metal stamping industry. Our closed-loop development process allows us to take a part from concept to production more efficiently and cost-effectively than our competitors.
Prototyping and Testing
Our advanced prototyping and testing capabilities ensure that every product meets the highest standards of quality and performance. By utilizing state-of-the-art technology and rigorous testing procedures, we can quickly iterate and refine designs to meet the exact specifications of our clients.
Custom Tooling Solutions
MES offers custom tooling solutions designed to meet the specific needs of our clients. Our experienced team uses advanced CAD software and precision machining techniques to create high-quality tools that ensure optimal performance and durability in production.
Material Expertise
Our expertise in material science allows us to select the best materials for each application, ensuring maximum efficiency and performance. Whether it’s lightweight composites, high-strength steel, or corrosion-resistant alloys, MES provides solutions that meet the specific demands of each industry.
Sustainable Practices
We are committed to sustainability and environmental responsibility. Our product development processes are designed to minimize waste and reduce environmental impact. By implementing sustainable practices and using eco-friendly materials, we help our clients achieve their sustainability goals.