Advanced Simulation and Design
Utilizing our in-house FEA software (PamStamp), we are capable of conducting full product and process simulations. This advanced capability allows us to predict and resolve potential issues before they arise, ensuring that our tooling designs are optimized for performance and efficiency. Our seasoned tooling design engineers use SolidWorks software to create detailed and accurate designs tailored to each client’s specific requirements.
– Progressive, Transfer and Line Tooling
– Tooling Repair and Maintenance
– Dedicated Tryout Presses
– High Speed Machining Centers up to 60” x 30” x 30”
– Wire EDM 20.5” x 14.5” x 12.2”
– Waterjet 48” x 96”
– CMM Capabilities Utilizing PC-DIMIS
– 7 Axis Laser Scanner; Cloud Point Inspection for Validation or Reverse Engineering Scanning
– Design Utilizing Solidworks and AutoCad
– FEA Software; AutoForm and PamStamp
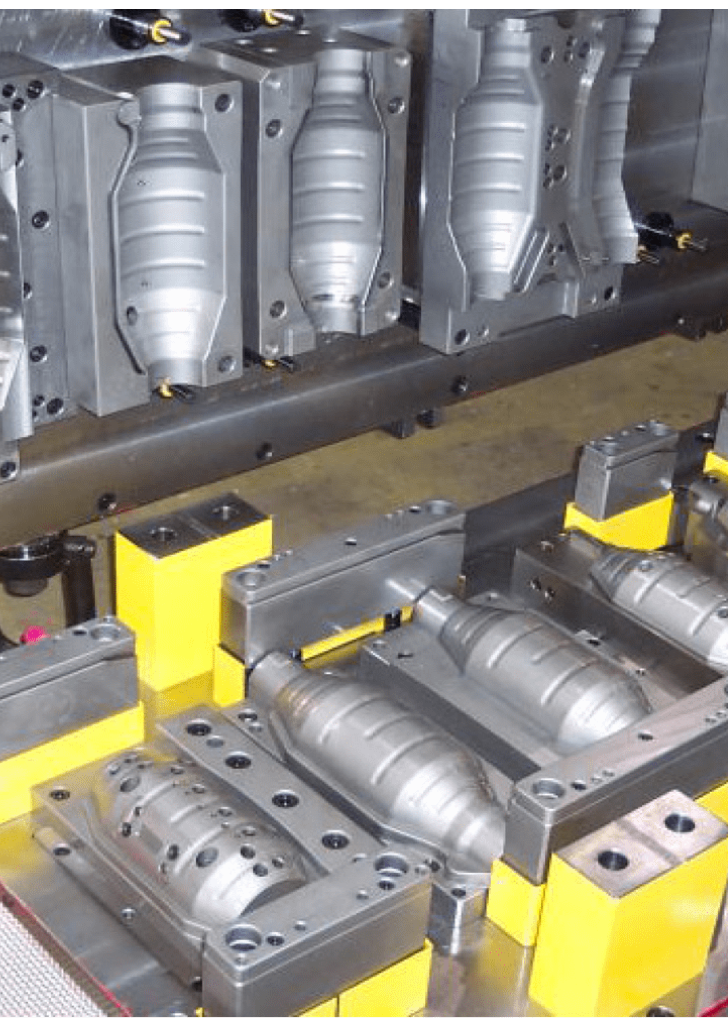
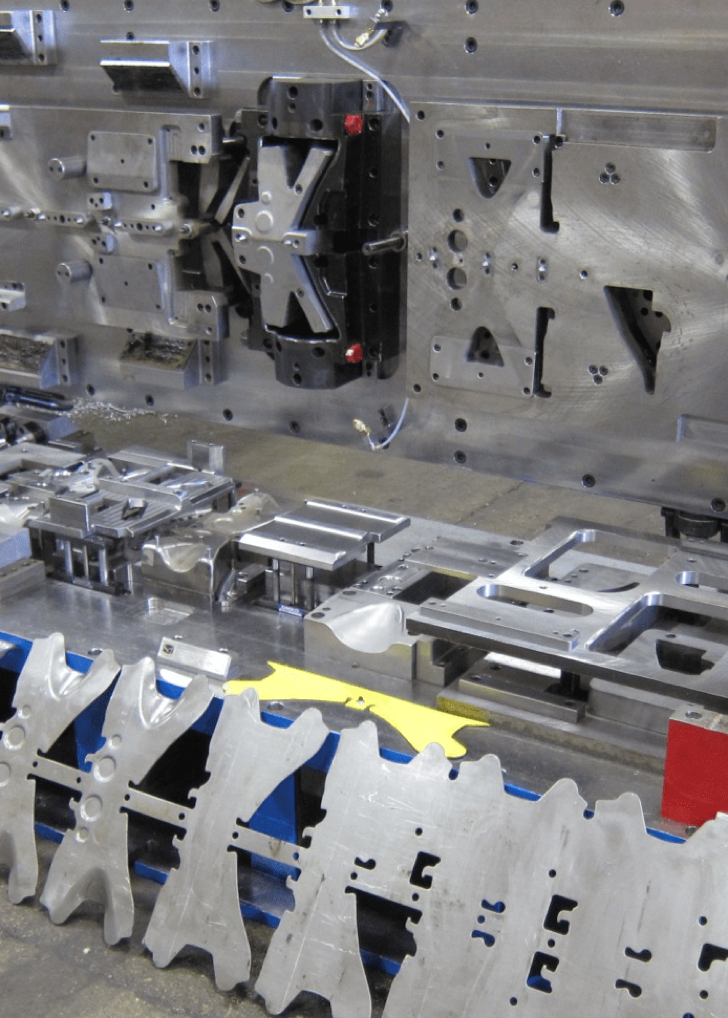
Partner with MES for Your Tooling Needs
Partnering with MES for your tooling needs means gaining access to a team of experts dedicated to delivering the highest quality solutions. We are committed to helping our clients achieve their manufacturing goals through precise, reliable, and innovative tooling. Contact us today to learn more about our tooling services and how we can support your projects.
Collaborative Design Review Process
Our structured design review process involves input from a cross-functional team of designers, tool makers, engineers, manufacturing, and quality experts. This collaborative approach ensures that every proposed process meets or exceeds the most stringent requirements. By leveraging the diverse expertise of our team, we can guarantee that our tooling solutions are both innovative and reliable.
Custom Tooling Solutions
MES provides custom tooling solutions designed to meet the unique needs of our clients. Whether it’s progressive dies for high-volume production or specialized transfer dies for complex parts, our tooling solutions are engineered to deliver exceptional performance and durability. We work closely with our customers to understand their specific needs and develop tooling that enhances their manufacturing capabilities.
Commitment to Quality and Precision
Quality and precision are at the core of our tooling services. Our rigorous quality control processes ensure that every tool we produce meets the highest standards. By using advanced simulation and design techniques, we can deliver tools that provide consistent, reliable performance, reducing downtime and increasing productivity for our clients.